Modular Homes Surpass Stick Built Homes
DEAR TIM: I have heard horror stories about custom homes that have taken forever to build. Framing lumber exposed to the elements can support mold growth.
Construction delays can create extra loan interest and living expenses. What can I do to make sure my new custom home gets built quickly but with no sacrifice in quality? Is there an alternative method to achieve my goal? Ted S., Lumberton, NC
DEAR TED: If you would have asked this question ten or fifteen years ago, I would have told you that you have little hope. Don't get me wrong, there have always been highly skilled and productive builders in the marketplace. You can find them in just about every city or town. I will grant you, however, that they are a very small minority. The good news for you, and many others, is that cost savings, high quality, and lightning-fast construction are present in today's new home marketplace.
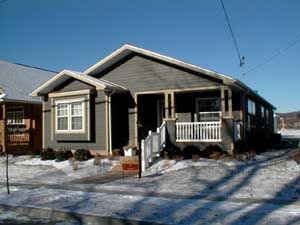
Yes, this home arrived at the jobsite pre-built on the back of several flatbed tractor trailers. You would never think it was possible when you walk up to it and inside of it. I did both as this fantastic home is just several miles from where I live.
Let's talk about conventional home construction practices first. Understand that many builders have never had extensive formal training with respect to manufacturing processes. After all, they are manufacturing a product. It is common for builders to start off in their careers as carpenters who transform from a subcontractor into the person who runs the show. Many of these individuals do not have strong technical and business skills in the actual art of planning and management. I know there are builders who have strong college business degrees, but I believe you will find that many smaller custom builders have minimal college level business classroom experience.
Add this to the mix of subcontractors who have work commitments with other builders, weather conditions that can hamper construction, scheduling and ordering mistakes on the part of the builder and a myriad number of other variables and you can see why a five month construction time frame can become a bloated nine or ten month fiasco.
If you decide to use a traditional custom home builder, you can tighten up the schedule and possibly get the job done on-time if he is familiar with critical-time-path planning. A home building project can be represented on a chart that shows each task that must be completed, the amount of time it takes to do that job and when certain tasks can happen simultaneously. If the correct data is put on this chart and all sub contractors hit their mark, you can get a traditional home built in a minimal amount of time. But that being said, always remember that Mother Nature bats last. She can throw multiple curve balls that will retire the side causing weeks of delay.
Imagine if I told you that you could actually save considerable money, get your home built in weeks instead of months, and have just about every item in the house you want all with no sacrifice in quality. Millions of people such as you can get a new home that looks and is identical to any traditional site or stick built home but believe it or not, it is trucked in cubes or modules to the jobsite. I urge you to begin talking with a modular builder in your city or town.
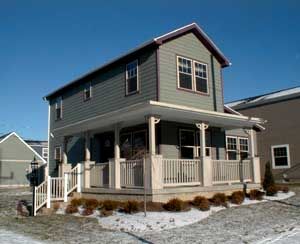
Check this out! A two-story modular home. It looks as retro as can be. You would think this home is 90 years old based upon its style and architecture. But is is modular and less than one year old.
Modular homes are built in factories that are climate controlled. The homes are assembled with enormous precision and quality. The same or better materials are used that a traditional site builder might use. The work force shows up on time each day at the modular factory. They are team players that know exactly how each home is to be built. The entire process is computer controlled down to the hour. Modular homes meet or exceed just about every local building code. Incredible as it may seem, the interior of each module is finished before it is trucked to the jobsite. Walls are painted, cabinets and tops are in place, flooring is complete, etc. I suspect if you asked for it, the factory might even stock the pantry with dry foodstuffs!
I have inspected many modular homes. The workmanship astounds me. The level of quality is higher than a vast majority of traditional site-built homes. Perhaps the most unbelievable aspect is the cost savings. As modular homes get bigger, the price compared to traditional site-built homes goes down. For example, if you plan to build a 4,000 square foot custom home, a modular home that is identical in every way might cost you 20- 25 percent less. That can translate to savings of possibly $80,000.00 - 100,000.00! The break-even point is about 1,500 square feet. If your planned custom home is larger than that, expect to save money and time but no loss of quality.
Column 449
One Response to Modular Homes Surpass Stick Built Homes