Building Product Defects
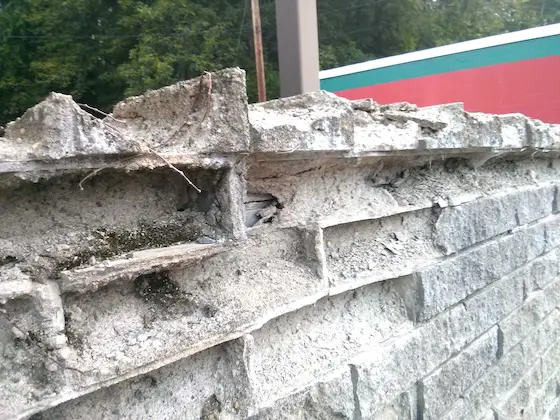
Building product defects - The sand and small rocks used to be solid concrete blocks. They failed because of a manufacturing defect. The mortar used to lay them didn’t fail. Copyright 2025 Tim Carter
Building Product Defects Happen All the Time
Building product defects can sap money and energy from you. Building materials made in factories can contain latent defects. These are hidden time bombs that can explode causing mayhem in your life. It’s not easy to spot them, but there are some things you can do to prevent both physical and financial harm. I’ve dodged the bullet several times in my career and lifetime.
Several decades ago I built a stunning Queen Anne Victorian replica home for my family. I purchased top-quality windows made by a major brand. These windows looked exactly like ones you’d see in a home built in the late 1800s including the distinctive extended window-sill horns that the exterior trim rested upon.
About ten years after they were installed, I was reading the latest issue of the Journal of Light Construction. I subscribed to several building magazines to help stay abreast of the latest products and building techniques.
Defective Clear Wood Preservative
There was a very tiny announcement about the major window brand filing a huge lawsuit against a national paint company. The lawsuit alleged that the paint company supplied the window manufacturer with a defective clear wood preservative. The window company used this preservative to prevent wood rot in both the window frames and the sashes.
My windows contained this invisible defective preservative. The window company sent out one of their engineers to confirm this. Wood rot was discovered in all of my windows. The window company supplied me with new windows and a cash settlement to install them. I was also reimbursed for all the required exterior and interior painting. To say the least, I was very lucky. Without this settlement, it would have cost well over $50,000 to replace the rotting windows.
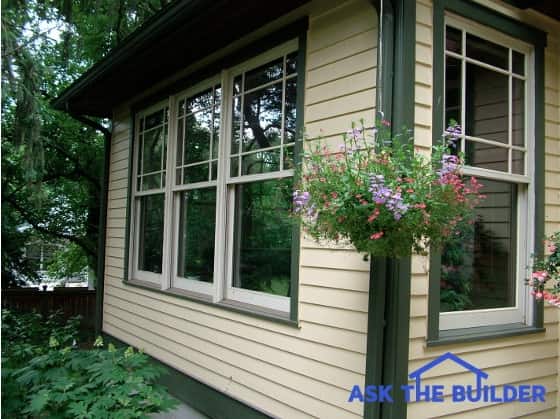
These are the new replacement windows I had to install after the original ones rotted out. Copyright 2025 Tim Carter
Not too long ago I met a friend at a restaurant here in New Hampshire. A concrete block wall separated the parking lot from an outdoor patio. The top courses of the concrete block had disintegrated, and were nothing more than sand and small stones. There was not enough cement in the block to resist the freeze/thaw cycles experienced each winter.
The lack of cement in the block could have happened because of a malfunction in the batching machinery that measures out the quantities of sand, small stones, and cement. It’s also possible there could have been enough cement, but the dry mixing process didn’t distribute it evenly. Finally, too much water might have been added to the mix. The failure could have been one, or several, of these possibilities.
Composite Deck Railing Defect
My most recent encounter with defective materials happened on my own outdoor deck. Several years ago I installed a composite decking and railing system made by one of the top deck manufacturers. I took great care to install the materials following the manufacturer’s instructions. I even had their local factory rep stop by to offer up suggestions before I started the work.
The round aluminum balusters in the railing were held in place by plastic extrusions that fit into the top and bottom fiberglass railing members. The day I installed them they fit perfectly with no gaps where the extrusions touched the vertical railing posts.
Two years later I was out on the deck one day and noticed a 1/4-inch gap between the end of one of the extrusions and a post. I then took the time to look at all of them. Much to my surprise, there were huge gaps everywhere. The 8-foot-long extrusions were now 3/4-inch shorter than when I installed them. It was a summer day, and if anything, the extrusions should have been longer as the plastic has a significant expansion coefficient.
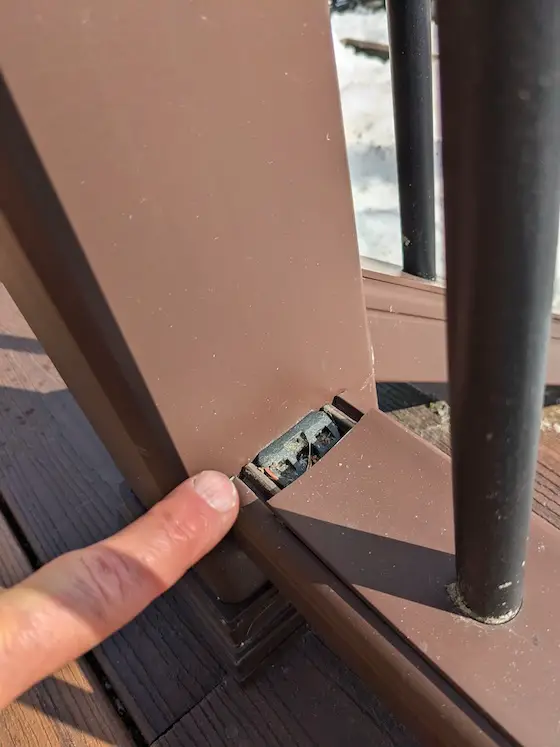
The flat plastic extrusion that has holes for the round balusters used to touch the deck post. Look at the 3/4-inch gap! Photo credit: Tim Carter Copyright 2025
I reached out to the manufacturer. They admitted they had a manufacturing defect that caused the extrusions to stretch as they inched their way out of the molding die. After a few years, the plastic shrinks back to what it should be. That’s not a good thing for folks like you and me!
The manufacturer sent me all new extrusions to replace the defective ones. I decided to wait a year or so before installing them just in case they decided to shrink in the box!
Use Time-Tested Materials
What can you do to prevent situations like I’ve experienced? When it comes to buying wood windows, it’s not easy. Most come primed from the factory. A builder will almost never invest the time to paint the windows with finish paint before they’re installed. It’s an enormous amount of work, but you can remove the plastic jamb liners and paint all exposed surfaces of the entire window frame. You can caulk any hidden joints where water might soak into the end grain of the wood.
Instead of using concrete blocks made in a factory, consider using natural stone made by Mother Nature. She’s been doing it so long that she’s perfected making building materials that can last millions of years. Granite, sandstone, and limestone can last for many thousands of years in the harshest climates.
As for plastic deck railing components, I’m not sure there’s an easy answer. I would defer to railings you might find in older homes such as wrought iron. Invest in time-tested materials where you know the cost to replace something is both difficult and time-consuming.
Column 1603