Concrete Block Crumbling
DEAR TIM: I own a diner where decorative concrete block forms the lower part of the exterior walls. At the front of my building, a wing wall extends away from the building. Some of the solid concrete block are crumbling away to nothing while others adjacent to them appear to be in perfect condition. The cap block at the top of the wall are showing the worst deterioration. These block are less than fifteen years old and the builder assured me they'd last at least 100 years. Why are they failing, what's the best way to repair them and how can I prevent failure in the future? Marty S., Concord, NH
DEAR MARTY: Wow! The photo you sent really shows the damage. Isn't it incredible that the mortar joints between the block are still in great shape while the block is crumbling? That's a significant clue as to why the block failed.
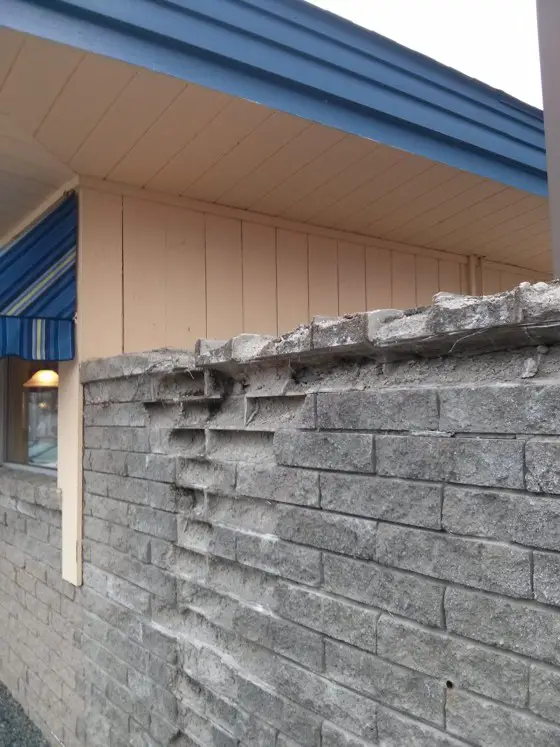
Some of the concrete blocks in this wall are beyond repair. The mystery is why only some failed. Photo Credit: Marty S.
Concrete block is a great material when it's made correctly. It's artificial rock when you think about it. Your builder's statement about it lasting at least 100 years is not far off when you look around you. With minimal effort, I can show you concrete walls built by railroad companies that have been exposed to harsh winter weather and the walls look much like the day they were poured.
To understand why some concrete can last so long and other crumbles in a short amount of time you just need to think about how concrete is made. The most basic concrete has just four ingredients: rock, sand, water and Portland cement. All the ingredients are important, but only one is responsible for the long-term durability of the concrete and that's the Portland cement.
In the case of the railroad bridge abutments that are over 100 years old and in great shape, I'm sure the reason is because the builders added extra Portland cement to make it extremely strong. The current minimum requirement for exterior concrete is to make it so it's a six-bag mix or tests out to 4,000 pounds per square inch (PSI) of compression strength. Nothing says you can't add more cement to get to 5,000 or 6,000 PSI!
There are many possible reasons why the concrete block crumbled and it's virtually impossible to point to the smoking gun. It could be that when the concrete block were made, that portion of the mix didn't get thoroughly blended. It's possible that the batch was mixed correctly but extra water was introduced into the block that are deteriorating. That extra water can dilute the amount of Portland cement in the mix.
It's also possible the failed block were not cured properly and the water in the block evaporated too quickly. This water is required to fuel the continuing hydration chemical reaction that causes the billions of microscopic cement crystals to grow and interlock with the sand and rock. If concrete is not cured correctly it never attains its design strength. I could go on and on with other possible causes, but those are the top ones I feel might be the cause.
The fact that the mortar in between the block is still there and in great shape tells you that it's not just a simple matter of the wall getting wet and then repeated freeze / thaw cycles blew it apart. If that was the case, the mortar would probably be rotten as well.
The repair process is not too hard at all. It's just time consuming. Any seasoned mason can do the repair. The key is obtaining concrete block that match in color so the repair doesn't stand out like a sore thumb. This is a perfect example of why I always tried to order a few hundred extra brick or block for my jobs and leave them behind for the owner. Wouldn't it be nice if you could just go grab the extra ones the builder left behind?
You'll want to pay attention to the existing mortar in the wall near where the failed block are located. Look at the mortar very closely, even with a magnifying glass. You should be able to see individual grains of sand. Note the size and color of the sand particles.
When mortar is fresh and new, the cement and lime paste coat all the sand and mortar looks uniform in color. But after a few years Mother Nature erodes and washes off the thin gray mortar paste revealing the sand. This sand makes up close to seventy percent of the matrix of what you see, so the color and size of the sand particles must be matched if at all possible.
I'm sure the sand came from a nearby sand and gravel pit, so go get some brick sand from the pits, allow it to dry and see if it looks like the sand you see in your mortar joints.
Once the mason repairs and lays the new block, keep the mortar damp for at least a week if possible. After that allow the repaired area to sit for another four weeks. At the end of the wait period, wash the wall with a dilute solution of muriatic acid and water. This will help wash off the mortar paste revealing the sand in the repaired joints.
You then want to coat the entire wall with a silane-siloxane water repellent. These are readily available both online and from specialty stores that sell products to brick and concrete masons. Beware some of the highly advertised products you see on TV as these are not silane-siloxane products.
Pay attention to the label on the water repellent you purchase and follow the instructions to the letter. Some require two coats be applied within so many minutes of each other. To get fantastic penetration of the sealer into the wall, have a helper with you. As you apply the sealer with a hand-pump garden sprayer, the helper uses a powerful leaf blower to blast the wall right behind you. This air pressure drives the sealer deep into the mortar joints and the block. Don't skip this important step.
Column 1110
7 Responses to Concrete Block Crumbling