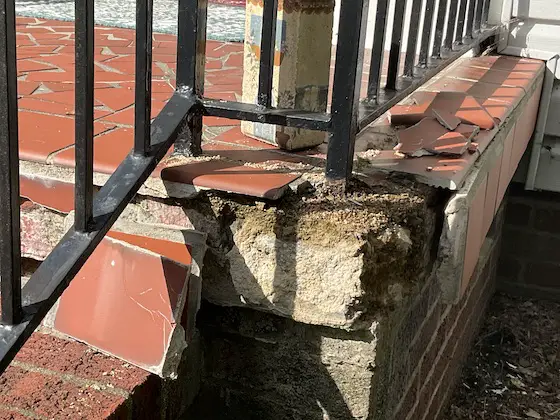
This porch was constructed in 1949. Its best days are undoubtedly behind it. Copyright 2023 Tim Carter
Repair Front Porch - Mosaic Tile and Concrete Base
In the past week, Don asked me for advice. He lives in the extreme northeast corner of North Carolina just 15 miles from the Atlantic Ocean. His front porch stoop is in very bad shape. Back in 1949 when the house was built, the tile setter used quarry tile to create a mosaic look on the flat surface. He then mortared full tiles to the sides and front of the poured concrete stoop.
Don shared that the repairmen he’s talked with are very nervous as to how to proceed. Some of the mosaic tiles are cracked and when you tap on some tiles it produces a hollow sound. Many of the full edge tiles are falling off. In other words, the 74-year-old porch is in poor condition.
Don mentioned that he and his wife want to keep the original look and he wondered what might be the best plan of attack. Based on the photographs he sent, my opinion is it’s time to get rid of all the old tile and rotten concrete base beneath the tile.
If Don hired me to do this job, the first thing I’d do is take photographs of the mosaic tile layout that forms the flat surface of the porch. If there was enough money in the budget, I’d create a map of the mosaic tiles. I’d take the time to trace the pattern of the tiles onto construction paper. These templates of each of the pieces of the random-shaped tile would be numbered and put on the map.
I know this is obsessive-compulsive, but if Don and his wife wanted the exact same look and money was not an object, then this is exactly what should be done. I’ve worked for customers in the past that had these financial resources. While it’s rare to have a budget that will allow this, I have to tell you it’s intensely rewarding work.
There are many possible reasons why Don’s porch fell apart. The truth be told, there’s no reason why it shouldn’t have lasted 150 years or more. For starters, Don lives in a very mild climate. While it does get cold and the temperature drops below freezing in winter months, it’s not the extreme cold I suffer from where I live in New Hampshire. It could even be worse had Don’s house been in International Falls, Minnesota!
I’m quite sure if I visited Don’s city I could locate several railroad bridges that were constructed in the early 1900s. The concrete abutments supporting the bridge beams are probably in good or very good condition. I can take you today to similar ones in Cincinnati, Ohio that suffer from much worse weather than what Don experiences. These railroad structures are in great condition.
The reason the railroad bridges are in such great shape is because the bridge engineers and designers specified that lots of Portland cement be used in the mix. Today the minimum specification for most exposed concrete is 4,000 pounds per square inch (PSI) or a six-bag mix. This means six 94-pound bags of cement are in each cubic yard of concrete. You can always add more cement. The cement is the glue that holds together the sand and stone in the concrete.
I would order an 8-bag mix for Don’s new concrete stoop. This might elevate the strength up and over 6,000 PSI. I’d also be tempted to add a bit more pure Portland cement to the thinset mix used to bond the new quarry tile to the concrete.
There are a few other things I’d do if Don hired me. For starters, I’d tell Don that the best weather to install the concrete and tile would be in the fall or spring. I’d want daytime temperatures to be around 60 F with no threat of rain. I’d want the nighttime temperature to not drop below 45 F.
I’d precut all the new mosaic tile and lay it out on a flat surface that matched the size of the new porch. I’d want to make sure all the tile were the correct size. This would be done before the new concrete porch stoop was poured.
I’d pour the new concrete porch late in the day on a Monday or Tuesday. I’d plan on installing new tile on the concrete the next morning at 7:30 AM. Cement paint would be used as a bonding agent between the fresh concrete and the thinset mortar. You add clear cold water to Portland cement mixing it to the consistency of gravy to create cement paint. I was taught to do this by wise concrete masons who applied cement stucco to exterior steps in Cincinnati many years ago.
Once the tiles were all set, I’d cover the tile with plastic to help retain the moisture in the fresh thinset and concrete base. I’d wait at least 48 hours before I’d think about grouting the tile. Once grouted, I’d cover the porch and edges again with plastic to hold in the moisture. I’d not take the plastic up for at least three days.
The concrete stoop, the thinset, and the cement-based grout all need water to cure properly. If water leaves these things too rapidly, they never attain their desired strength.
A month or two after the porch was finished, I’d apply a clear silane-siloxane sealer to the new porch. This would minimize water infiltration into the grout. Water that seeped into the grout and original concrete is what destroyed Don’s porch. Don’t let it happen to you.
Column 1526