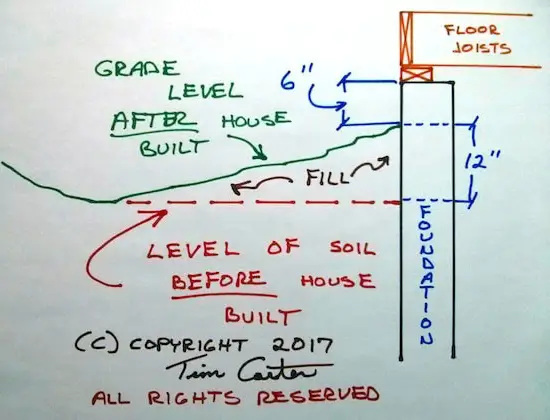
This simple drawing shows that a foundation must be 18 inches higher than the highest point of grade on the lot within 10 feet of the foundation. Copyright 2018 Tim Carter
Foundation Height TIPS
- Old builders knew best
- No window wells
- 18 inches minimum - SEE drawing
- The building code is minimum - exceed it
- CLICK HERE to Get Tim's FREE & FUNNY Newsletter!
Did Dead Builders Know Best Foundation Height?
If we could conjure up the spirits of several custom home builders who've been dead for about 100 years, I am afraid they'd be most disappointed.
No doubt they would shake their heads when they gazed upon house after house in the modern suburbs in many cities that had the top of their foundations skimming just above the final grade of the soil that surrounds each house.
In fact, we might even hear them mutter, "What was that builder thinking..."
History, Legend & Myth
Did you read J.R.R. Tolkien's book Lord of the Rings? It was made into a great three-part movie.
At the beginning of that movie is a fascinating quote taken from J.R.R. Tolkien's book:
"And some things that should not have been forgotten were lost. History became legend. Legend became myth. And for two and a half thousand years, the ring passed out of all knowledge."
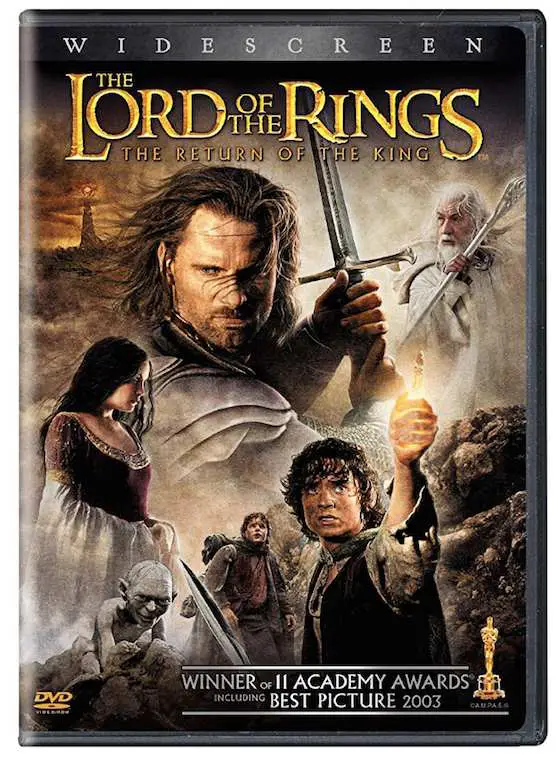
You can discover much about life and how to build castles that withstand dragon fire watching this movie. Great love story too. CLICK HERE NOW TO ORDER THIS MOVIE IN ANY FORMAT.
For the most part that's what's happened with the knowledge of foundation heights. Who knows, I may be the last bastion of this nugget of building gold.
CLICK HERE to get FREE & FAST BIDS from local builders. Show them this column.
There are many things about building that are taken to the grave with builders and remodelers. It's unfortunate because most don't spend the time to record what they know for future generations.
The Internet, with comments on pages and videos, is helping to slow the loss of information, but the trouble there is much of the information is incorrect, incomplete or written so poorly as you can't understand what's being said.
When Should I Talk to My Builder About Foundation Height?
If you're in the planning stages of building your new home and/or are talking to various custom home builders about a new home, you need to talk about foundation heights. This topic simply deals with the distance from the top of the foundation down to the finished grade that touches up against the foundation and the soil within 10 feet of the foundation.
It may not seem important to you now, but once you are moved in and it rains hard for several days, you will wish foundation height would have been just above "How big will my kitchen be?" on your top-ten wish list.
What is the Ideal Foundation Height?
Look at the below crude drawing I made. The bottom of the green swale should be about ten feet away from your house foundation wall.
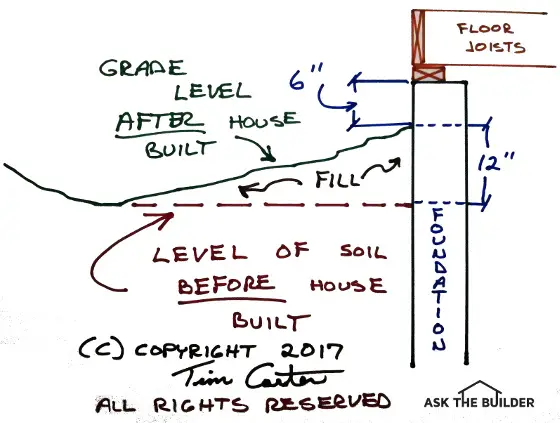
I made this drawing. You can see the foundation wall with a typical sill plate and floor joist. The red line is the lot before the excavator shows up. The top of the foundation should end up 18 inches ABOVE the red line. Use the dirt from the hole to create the slope away from the foundation. (C) Copyright 2017 Tim Carter ALL RIGHTS RESERVED
How Smart Were Old Builders?
I'm constantly amazed at the intelligence of many old builders who have departed this world. It's indeed a shame more builders do not "build them like they used to".
Drive around the older sections of your city and you'll undoubtedly see homes where the first floor level is two or even three feet above the ground outside the home. Often these homes have steps that lead up to the front door. They often have dramatic front porches where you can sit and gaze down upon the gorgeous neighborhood.
CLICK HERE to get FREE & FAST BIDS from local builders. Show them this column.
Why Were Old House Foundations Higher Out of the Ground?
I firmly believe this was done for several reasons. Powered excavating equipment was not available or readily available. It was less expensive to dig shallower foundations.
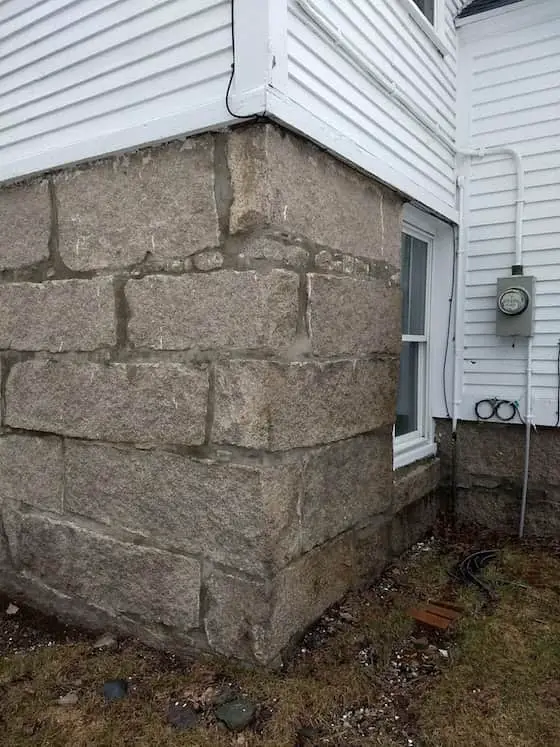
This is an old stone foundation on Mt. Desert Island in Maine. Note how high out of the ground it is. Smart builder indeed! Copyright 2018 Tim Carter
Foundation walls that protruded above grade allowed basement windows to exist without the modern sunken semi-circular window wells. These exposed windows could let in more light and ventilation into the basement. The dirt removed from the excavation could be gently graded away from the house to create wonderful positive drainage.
Did Wood Rot Happen?
Rainwater that splashed on homes rotted those close to the ground. It didn't take smart builders long to figure out that if you kept the wood up about 30 inches from the ground, you'd have minimal, or no, rot.
This had to be another motivation to keep the foundation up out of the ground.
Are Newer Home Foundations Too Deep?
But scan the new homes in subdivisions today and you'll rarely see a home built this way. Is the new method better?
I think it's debatable, especially in light of the modern uniform building codes. The codes speak to foundation heights.
Typically the codes say the amount of exposed foundation should be between a minimum of 4 and 6 inches above the finished soil that touches up against the foundation. Remember this is a minimum distance.
The building code is actually a set of minimum standards. Many homeowners think just the opposite. Building your home to the code standards is like getting a 70-percent grade on a test.
What Does the Building Code Say?
Furthermore, the code will often state the ground around the foundation must slope away from the house. Read this code section and it will almost always say the ground must fall 6 inches vertically for the first 10 feet of horizontal distance away from the foundation. What do all of these numbers have to do with foundation height you might ask? Plenty!
CLICK HERE to get FREE & FAST BIDS from local builders. Show them this column.
Who Establishes Ground Height in New Subdivisions?
The developer of a subdivision establishes the finish grade of the lots before construction begins. The word grade references the level of all the ground on your building lot before you start to dig a hole for the foundation.
Builders need to be sensitive to these established grades. A good builder determines the highest point of ground near the home and sets the top of the foundation in relation to this high point.
What Happens if My Foundation is Too Low?
When a new home builder decides to set the foundation height too low, all sorts of problems happen. The ground around the home tends to be very flat.
Positive drainage is either minimal or may not meet code. Sidewalks leading from driveways to the front door can act as dams trapping water movement away from a house.
These sidewalks become a barrier to establishing the needed positive drainage away from the house as they sit too high.
Can Mulch Create Water Dams?
The problem gets even worse when the landscapers show up. They'll often mulch in these areas and create negative drainage. Because mulch is piled up, the water in some areas around your home may actually drain towards the foundation!
You'd think this is all common sense, but the older I get the more I believe common sense is something that needs to be taught, not acquired by experience.
What is the Best Foundation Height?
Typically, I'd set all of my foundation heights about 18 inches higher than the highest point of grade within ten feet of the finished foundation. Doing this allowed me to create 12 or more inches of fall within the first ten feet of horizontal distance.
It also produced 6 inches of exposed foundation above the soil around the home. Remember, you can put the foundation up higher to get more slope!
Are Gentle Slopes Possible?
I'd use some of the excavated soil to create gentle slopes away from the house in as many directions as possible. When done properly, these slopes did not interfere with the grade established by the developer.
Houses built in this fashion do not appear to sit high out of the ground. They appear stately as they sit on the artificial rise you create with the dirt that's brought up from digging the foundation.
What's more, the house sports positive drainage from all sides so that flooding rains do not inundate the basement space.
CLICK HERE to get FREE & FAST BIDS from local builders. Show them this column.
Column NH001