Hot Garage Ventilation Checklist
DEAR TIM: The garage attached to my townhome gets the full afternoon sun. The temperature in the garage has reached 110 degrees at times this summer.
There's some attic space above the front half of the garage and two bedrooms over the rear half of the garage both of which get very warm during the summer.
Would an insulated garage door help keep the garage cooler, or is there a way to vent the garage to remove some of the hot air? I have a roll-down screen, but in the summer it does not seem to offer much relief from the heat. Jan McM., Largo FL
DEAR JAN: No wonder your garage is an oven.
Is West Facing Garage the Worst?
You garage west-facing orientation couldn't be worse. As the day progresses and temperatures climb, they often peak between 4 and 5 p.m. This is exactly when the direct rays of the sun are cooking everything they shine upon including your garage and everything inside it.
Free & Fast Bids
CLICK HERE to get FREE & FAST BIDS from local fan contractors.
Do Cars Add Heat to a Garage?
Yes, cars that have been out on the road and then park in a garage add considerable heat to the space.
All of the car's mechanical parts can be very hot after it has been driven for just 10 or 15 minutes in the summer months.
Some of the parts, like the disc-brake rotors, can easily be in excess of 250 F. The car will radiate heat into the garage for hours after it's parked.
Does the Concrete Floor Store Heat?
If the sun beats on your concrete floor, it acts like a massive heat sink. I've tried to walk across concrete in the middle of summer with bare feet and scorched the bottoms of my feet.
You can imagine how much heat the concrete collects from the sun and then releases it later.
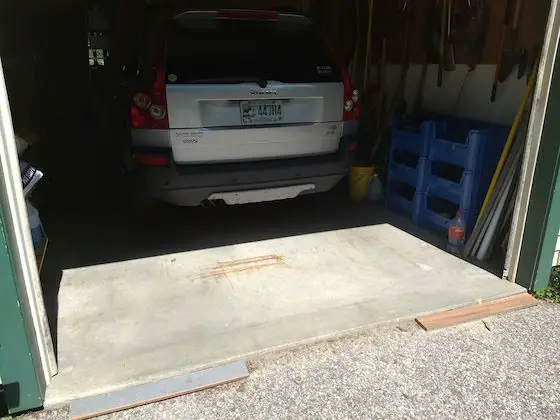
The direct sunlight is cooking the concrete floor raising its temperature. Look at the infrared photo just below to see how hot the concrete is! Copyright 2018 Tim Carter
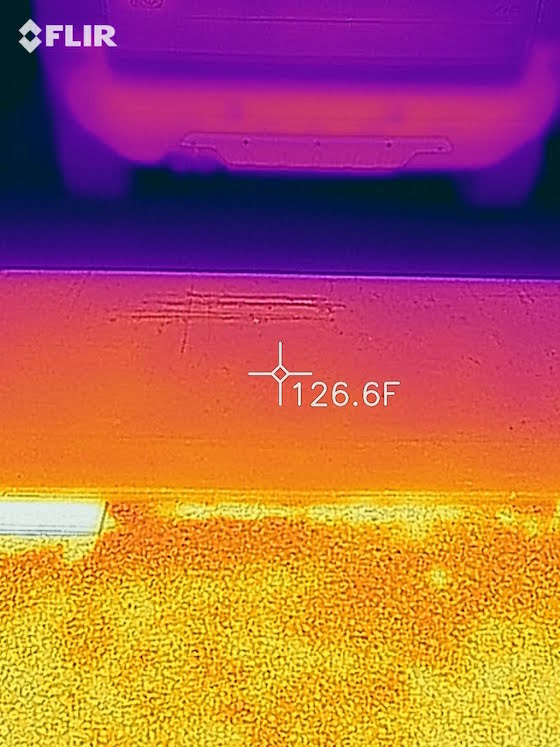
The concrete is already 126+ F and it's just after noon. After a few more hours, it's going to be getting up or over 140 F! Copyright 2018 Tim Carter
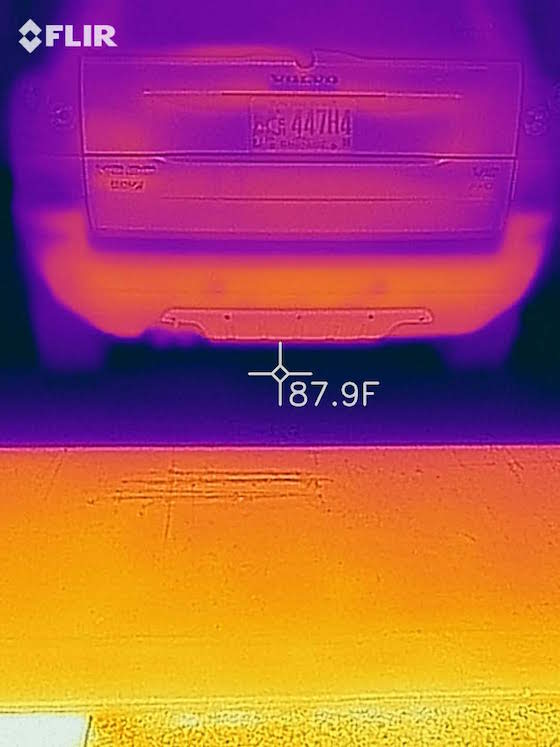
Look at the difference! The concrete under the car in the shade is only 87.9 F. You can see why you want to keep the concrete shaded if you want your garage cooler. Copyright 2018 Tim Carter
Does an Insulated Door Cool the Garage?
An insulated garage door can trap heat inside a garage. Insulation is designed to slow the transfer of heat.
If you were to install an insulated garage door and close it, you would trap this heat inside the garage where you do not want it. An insulated garage door may be a great idea for other times of year, it just becomes problematic in the summer months.
Does An Insulated Door Help in the Winter?
Insulated doors are excellent if you're in a cold climate and wanting to preserve car heat in the winter months. If you live in parts of the deep southern USA, Florida or the southwest where it rarely gets cold, I don't know if I'd get one if I wanted a cooler garage.
Do All the Contents of the Garage Radiate Heat?
Just as the metal parts in your car absorb and radiate heat, so do all of the objects in the garage. Think of how a dying campfire's embers and any rocks that surround it radiates heat for hours after the flames have stopped flickering.
How Long Will the Heat Last?
This low-level infrared heat can be felt inside a garage even early the next day. I know, as my own garage gets very hot in the summer months.
It's very common for my interior-garage temperature to be 10 or 15 F warmer than the outside air temperature when I go into the garage in the morning. The ceiling and walls of my garage are well insulated.
CLICK HERE to get FREE & FAST BIDS from local fan contractors.
Will the Garage Heat Rise to the Attic?
The heat from the garage will absolutely contribute to high temperatures in the attic space above as well as the finished rooms. Hopefully, the ceiling cavity between the garage and the finished spaces was insulted. If not, you may want to consider adding blown-in insulation.
Heat moves from hot places to cooler places. That's the basic law of thermodynamics.
This means if your garage is 110 F and adjacent rooms are 85 F, then the nearby rooms are going to be absorbing the heat. You can't stop this transfer.
What is the Best Garage Ventilation?
The best garage ventilation is lots of moving air. You want to bring in cooler air from outdoors into the garage.
To cool your garage as efficiently as possible, you probably will need to install one or two powerful sidewall ventilation fans. There are any number of fans designed to pull air through the garage and exhaust it back outdoors.
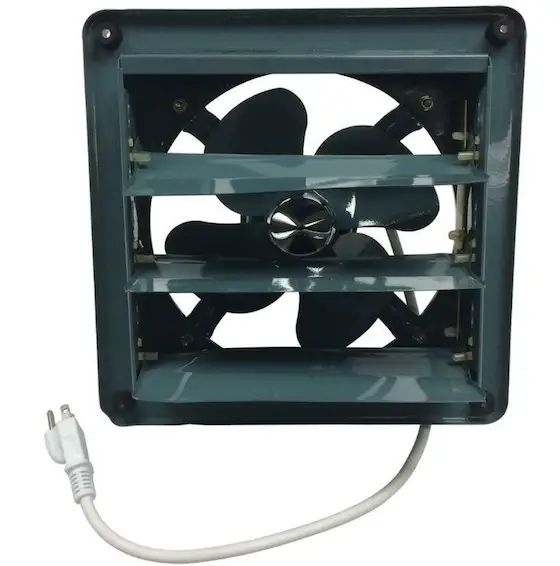
Here's a sidewall garage fan. It's meant to ventilate out the side of the garage. These come in different diameters. The bigger the blade, the more air it will move. CLICK THE IMAGE NOW TO BUY ONE.
How Cool Will the Garage Get?
The fans will not be able to drop the temperature lower than the outdoor air temperature. It may feel cooler to you as you stand in the path of the blowing air, but that's caused by the perspiration evaporating from your skin.
This means if it is 90F outdoors at 5 or 6 p.m., it will probably be in the upper 90's F inside the garage.
IMPORTANT TIP: The fans must have plenty of incoming air to feed their voracious appetites. You'll probably have to keep the garage door up off the floor about 4 inches to ensure plenty of air from outdoors is flowing through the garage.
The fans will do the best job of cooling if they're located high on the wall directly opposite the garage door.
The fans will pull the air across the garage if you have this orientation.
Will the Garage Contents Get Cool?
The air stream will seem very cool to you if you stand in it. But don't think the objects in the garage feel as cool as you do.
You feel cool because the evaporating perspiration on your skin is rapidly extracting heat from your body.
The inanimate objects in your garage do not sweat, so they will take a while to cool down.
Should I Install a Timer Or Thermostat Switch?
Consider putting the fans on a timer that allows them to run for several hours or use a thermostat to control when they go off. You can buy thermostats that will turn the fans on and off at predetermined settings.

This is a time-tested timer switch. You rotate the dial and it operates for how much time you choose. CLICK THE IMAGE NOW TO BUY IT.
How Big Should the Fans Be?
To do any appreciable cooling you're looking for ventilation fans that move thousands of cubic feet of air per minute. Always use price as a guideline.
Fans with well-balanced blades, high-quality motors and excellent exterior weatherproof self-closing louvers will always cost more. I urge you to buy as much fan as you can possibly afford.
Should the Fans Be on a Separate Circuit?
Yes, be sure the electrical wiring that's installed to make the fans work is a separate circuit and done according to all codes.
There's a good chance you'll have to install a new circuit or two if you buy large fans. They can draw a significant amount of electricity, and can overload existing circuits if you are not careful.
CLICK HERE to get FREE & FAST BIDS from local fan contractors.
Author's Comments:
The following are comments from several emails between Norm Sippel and Tim Carter, founder of AsktheBuilder.com.
Dear Tim,
"I faced a similar problem when I moved here three years ago. My hobby is racing vintage sports cars. I need to work on the cars year-round. Early in March of our first year here, I went to the garage (which faces east) at 10 a.m. I measured the steel door temperature with a pyrometer at 114 degrees. It was a radiator. No way I could work in those conditions in March, much less in August.
My solution - I insulated the garage doors (a double & a single) with 2" foam panels from a big box home store. I glued them to the panels between the ribs & under the beams. The few metal pieces that were still exposed were still hot, but closer to 100 degrees.
The ambient temperature in the garage dropped into the low 90s. I added blown-in insulation after that. Mid-summer the ambient temperature in the garage was down into the high 80s. Running two 5" air conditioning inlets into the ceiling that I can open if necessary dropped the temp even further. I keep them closed when I am not working in the garage & there is no return duct for safety reasons. This dropped the temp in August to the low to mid-80's. That's a tolerable temperature.
You are correct that bringing a hot car into an insulated garage will just keep it hot in there. The brake rotors you note as a major heat source cool a lot faster than the radiator, exhaust & engine do. But if Jan leaves the car out until after dark when it cools down (to the high 70s/low 80s here) before bringing it in, it will be a much-improved situation. And, the insulated garage door will do its job in the afternoon sun. That alone should lower the in-garage temperature about 15 degrees in the circumstances described."
(Tim Carter comment: I'm all for insulated garage doors, you just have to realize they block the heat transfer in both directions. The insulation holds in the heat overnight.)
"That's true. But, managing the interior temp is a lot easier when you don't have so many square feet of metal radiating heat to the interior.
Before I moved south, people said to avoid west-facing back-yards. I had hoped to find something where I could watch the sunset. Well, that didn't happen. I'm a mile inland from the Gulf. And, the back of my house with big sliders faces north. BUT, I have even bigger sliders that do face west. So, we have to deal with that. The best solution has been Queen Palm trees. In three years, they are tall enough that they shade the sliders by 4 p.m. in mid-summer.
"Here's a link to the magazine I work on: www.vintageracecar.com. But, in a previous business life, I worked for Fine Woodworking."
Norm Sippel
Palm Harbor, FL
Column 690