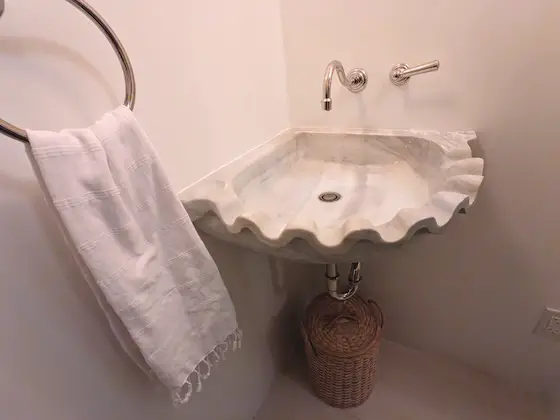
Unique Bathroom Sinks - This unusual corner shell sink with the minimalist wall faucet might be just what you’re looking for in your home.. Copyright 2025 Tim Carter
Unique Bathroom Sinks and Faucets Speak Volumes
It’s that magical time of year. The International Builders and Kitchen and Bath shows are just weeks away. This year this huge event is in Las Vegas. There are only a few convention centers in the USA large enough to house all of the exhibitors.
I’m blessed to be a member of the working press. As you might imagine, we’re treated like royalty at both shows. Just under two thousand companies want us to come to their booths to see all their new wares. I’ve been doing this for over three decades. You have to carefully pick and choose how you will spend your precious time.
Several manufacturers spend vast sums of money on their presence at the show. One is Kohler. Their booth is an oasis of eye candy if you’re entranced by anything to do with plumbing fixtures. I’ve been a master plumber for over forty years and have installed hundreds of Kohler fixtures. I always enjoy viewing the magnificent and elegant designs they debut at the show.
This is not to take away anything from the efforts of some other major brands like Moen, Delta, and American Standard. I happen to use a stunning Moen kitchen faucet each day here at my home to wash dishes.
This column is not a soft advertisement for manufacturers. It’s about how you can use some of their most unique products to set your home apart from your friends, family, and neighbors. Allow me to share a few stories that might inspire you.
Several years ago one company introduced a bathroom vanity faucet that looked like it was made in a rainforest. The spout appeared to be created from a stalk of bamboo. The handles were shaped like small bamboo stalks. My wife fell in love with it. I ordered one and installed it in our basement half bathroom. This faucet is still made today.
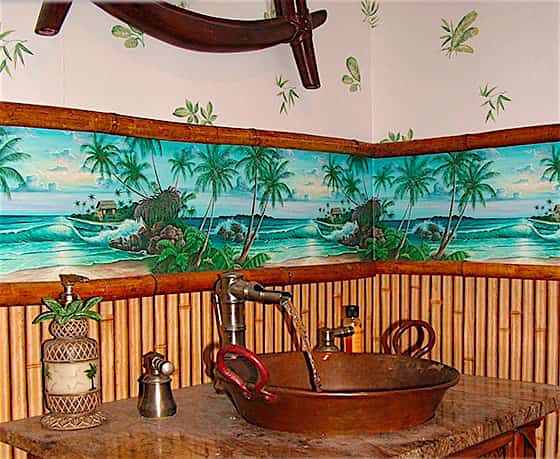
This is the bamboo faucet and copper basin. Copyright 2025 Tim Carter
The theme of the bathroom was tropical. We found two different wallpapers and a matching border that made it look like you were inside a grass hut with no glass. The openings gave you a view of the beach just beyond the palm tree line. The bamboo faucet sent water into a repurposed used copper basin. I drilled a drain hole into it creating a vessel sink that recessed into a stunning piece of brown variegated marble. You can use different faucets to create countless themes in your home.
My daughter did a similar thing in the half bath of her new home. The interior of her home was very contemporary. It had no woodwork surrounding the doors or windows. The wall board went straight down to the tile floors.
To extend this minimalist feel into her half bath, she found an antique wall-hung corner sink carved from a thick piece of marble. The artist created a scalloped curved front making the sink appear to be a giant sea shell.
I installed hidden L-brackets that were bolted to the sides of the wall studs. These extended out of the wall and the sink rested on them. The sink appeared to float in midair. The crowning touch was a single-handle wall faucet with a long gooseneck spout. Everyone that sees this sink marvels at it.
Do you think you could enlist the lowly ho-hum toilet to help create an illusion in a bathroom? My son is doing it now. He and I were forced to use a wall-hung toilet in a basement bathroom at his home.
Get the image out of your mind of the stark commercial wall-hung toilets you see in airports, office buildings, or schools. His toilet is a futuristic china fixture with smooth sides. As crazy as this sounds, it’s the most beautiful toilet I’ve ever seen. The water tank is hidden behind the tile wall. There’s a simple touch pad to activate the flushing action.
Are you planning to create a deluxe luxury shower in your home? Perhaps you’re doing a major remodel job or building a new home. Did you know you can install multiple shower heads to create a true rain downpour if that’s what you’re after? You can even include speakers that surround you with the sound of a rainstorm. The shower heads can be both in the walls or in the shower ceiling.
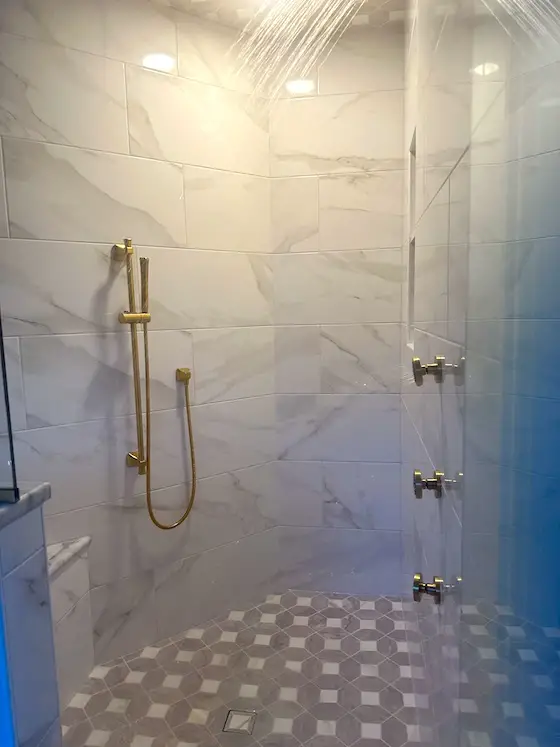
There's water flowing from the large shower head. However, as soon as you turn on the three body sprays water dribbles out of every orifice in this luxury shower. The East Coast plumber was a dunce. Copyright 2024 Tim Carter
Should you wish to do this, be sure you or your plumber does the math so you have plenty of water supplying your virtual reality shower experience. You may need to have 1-inch diameter cold and hot water lines feeding your bathroom. If you fail to do this, water may dribble from all the shower heads and body sprays.
You don’t have to have press credentials like I have to see all of these wonderful new products. At the end of February, YouTube will be flooded with thousands of videos shot at the show by members of the press. Search for IBS or KBIS 2025 videos.
You’ll be able to salivate over all the new kitchen and bath faucets from the comfort of your own home. You won’t have to be bumping into people in the crowded aisles like has happened to me too many times in the past.
Column 1595