Plumbing System Vent
Plumbing systems have been in use for thousands of years, however only in the past 100 years did they evolve as we know them today. Higher concentrations of people living in cities forced plumbers to become involved in sanitation.
Plumbers achieved a very high status in society 100 years ago, as they were responsible for public health. Because disease can spread easily and rapidly in water systems, it is important that individuals who work in these fields be regulated, knowledgeable and responsible. That is why plumbers are licensed in many states and cities.
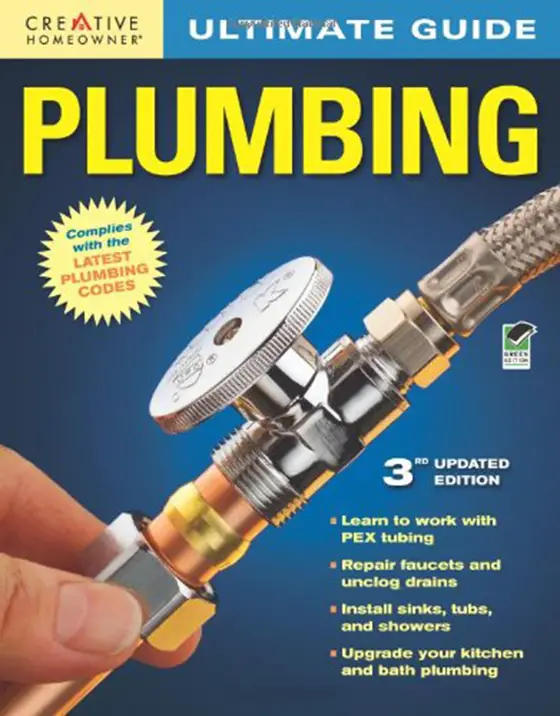
Want to know more about Vent Pipes and other plumbing topics. CLICK THE IMAGE to get the comprehensive guide to plumbing.
Plumbing system vents are an integral part of plumbing drainage systems. Many people do not realize the complicated nature of plumbing drainage and vent systems. A typical household drainage and vent system features two piping systems, both of which are interconnected.
One system (drainage or waste system) pipes water away from fixtures and conducts that water towards a sewage or septic system. The other piping system (vent system) supplies atmospheric air to each fixture.
CLICK HERE to get FREE & FAST BIDS from local Plumbers who can install your new fixtures.
Without vents, an interconnected plumbing drainage system will not work properly. Virtually every house in the USA has an interconnected plumbing drainage system.
Plumbing vents allow a drainage system to breathe. Sewage contains bacteria which creates obnoxious fumes. Besides supplying air to each fixture, a vent system allows those fumes to be directed to the atmosphere. The vent pipes are located on roofs, away from windows or other air intake devices, so that the fumes dissipate into the air.
Vent systems also perform another extremely important function. They allow for the equalization of pressure within the plumbing system every time water is poured into a sink or a toilet is flushed. To understand why this is important, you must realize the importance of the simple U- shaped trap beneath many of your plumbing fixtures.
U-shaped traps perform a vitally important function. These traps create a water seal. Usually, the depth of water in a trap is two to three inches. This water serves two purposes. Obnoxious gases and vermin within the drainage system cannot get past this water.
However, prior to vent systems, people discovered that if they rapidly drained water from one fixture, the water in the U-shaped trap of an adjacent fixture would be sucked away, leaving the trap dry. Fumes and bugs would soon enter the room. It didn't take long for plumbers to figure out that a vacuum was being created by the water traveling down the drainage pipes.
Plumbing drainage pipes are sized according to the size of the waste material and the quantity of water each plumbing fixture can handle. You don't want the pipe too small, as it may become easily clogged. On the other hand, you don't want a drainage pipe too large, as it may not be adequately flushed each time water drains from the fixture.
The pipes are sized so that if a sizable quantity of water is allowed to drain rapidly from the fixture, the drain pipe will completely fill with water. This is where plumbing systems without vents begin to get into trouble.
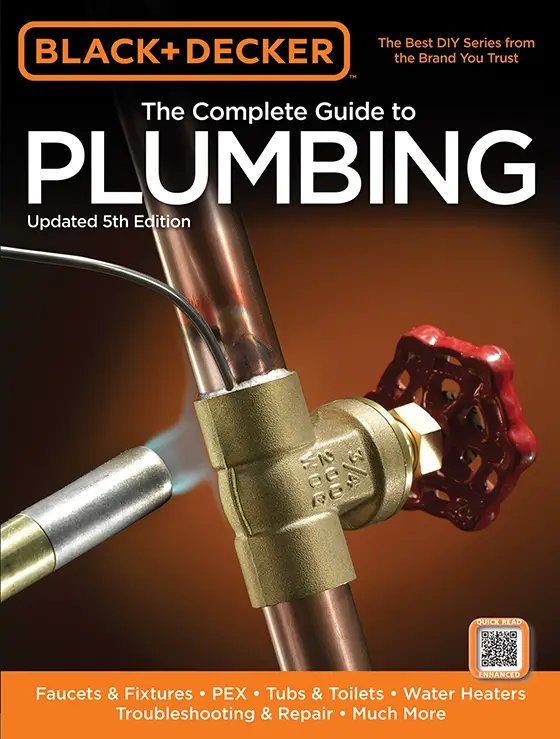
Need to fix your Vent Pipe or install a water heater? CLICK THE IMAGE to get a complete guide to all your plumbing needs.
Try to imagine the following scenario. A drainage system which is not being used has nothing but air in the pipes. The only water in the system would be that in the traps of the fixtures. Also, if you have never seen a plumbing drainage and vent system prior to the walls being drywalled or plastered, it looks very similar to a tree.
Just as the branches of a tree connect to the trunk, so to do plumbing lines. For the most part, all of the drainage lines eventually join together into one large pipe which exits your house.
OK, if you are still with me, here is the interesting part. When you allow a large quantity of water to be rapidly drained from a fixture, the drainage pipe just past the U-shaped trap fills completely with water. In some instances, as this water drains down through the system, the pipe continues to be filled with water.
The air that was in the piping system just before you pulled the drain plug is being 'pushed' ahead of the water. Because water is still draining from the fixture, the air can not be replaced at that fixture. That air must be replaced. If the system does not have vents, it begins 'looking' for air. As the water travels down the system, it begins to pass by other fixture pipes.
The surging water has created a vacuum immediately behind itself. As this vacuum passes by the other drainage pipes, the suction created by the vacuum can easily pull the water from the other fixture traps. As soon as it pulls enough water to break the water seal, air enters the piping system and relieves the vacuum. We already know why we don't want these water seals broken!
Vent systems eliminate vacuums. They do this very easily. Each of the plumbing fixtures in an approved drainage and vent system is served by a vent. This vent pipe is usually within three feet of the fixture.
The vent pipe's sole function is to supply air to the drain pipe of that fixture, in the event that a large quantity of water is discharged. Some plumbing codes allow multiple fixtures to be served by the same vent pipe. These are referred to as venting exceptions.
The installation of vent pipes is very technical. They also must be sized to permit a sufficient quantity of air to easily pass through them. They must be installed with a slope, just like drainage pipes. Water can easily condense within vent pipes.
This water must not be allowed to collect in a vent pipe. It should be able to drain readily to the drainage pipe system and then to the sewer or septic system. If a vent pipe becomes blocked with water or debris, the fixture, or fixtures, which it serves will be looking for other ways to get air when they need it. You don't want this to happen at your house.
CLICK HERE to get FREE & FAST BIDS from local Plumbers who can install your new fixtures.
Column B036
Watch this video to see how Tim SOLVED a problem in minutes!