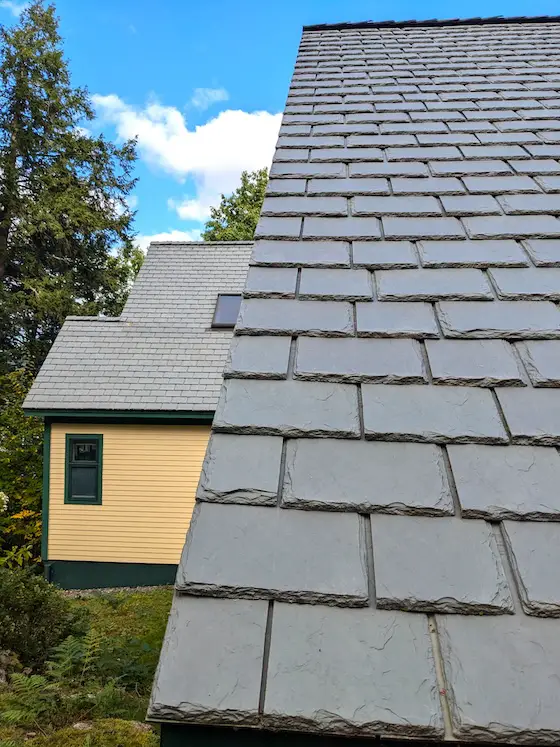
Asphalt Shingle Alternatives - This is not a slate roof but there’s a good chance you may be fooled thinking it is one. This is the DaVinci Roofscapes synthetic slate roof on my house. Copyright 2024 Tim Carter
Asphalt Shingle Alternatives - They Cost More But are Worth It
Are you about to install a new roof on your home or small business? The odds are you’ll be giving serious consideration to asphalt shingles. This building material has dominated the USA residential roofing market for just about 100 years. Go back farther in time and other, more durable, materials were the standard. Tin, slate, fiber cement, and tile could be found on even the most humble of houses.
Europeans Scorn Asphalt
European builders and roofers have reached out to me over the years. They’re shocked that we Americans even consider asphalt shingles. Some have told me that they’d not install asphalt shingles on the roofs of their dog houses.
Asphalt is scorned in many parts of the world because the people know how a roof is the second-most important part of a house just after the foundation. Those Europeans who reached out to me all said, “Asphalt shingles are a disposable material. Why would your homeowners even consider it?”
Asphalt is Cheap
The reason asphalt shingles are the king of the hill is simple. They’re cheap and if you can fog a mirror you can probably install them.
My Own Asphalt Roof FAILED
I was a fan of asphalt shingles for decades until I purchased my most recent home. I moved to New Hampshire and bought an eight-year-old house with a 30-year-guaranteed asphalt shingle roof. I thought at the time, “Well, that’s the last roof I’ll ever have.” Five years later, the roof started to experience a catastrophic failure.
Colored granules tumbled off my roof in the slightest breeze. After a rain shower, an avalanche would be on the ground. The shingles were curling and crumbling. I grew angrier by the day. Are you experiencing the same thing?
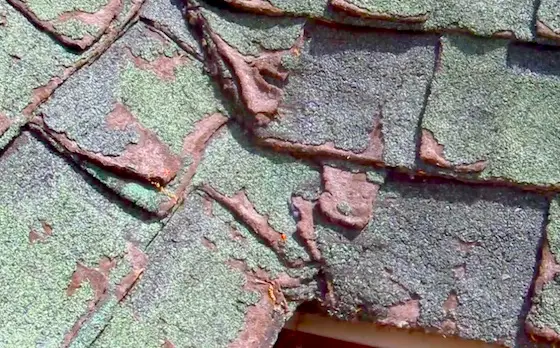
These are the defective shingles on my own home. Photo by: Tim Carter - Founder - AsktheBuilder.com
You may remember I did a national survey about failing asphalt shingles in the spring of 2015. I wrote a similar column back then sharing my tale of woe. A person deep inside the asphalt roofing industry saw my column, emailed me, and we had a one-hour phone conversation.
This person told me the deep dirty secrets of what was going on in the roofing industry at the time. He shared exactly why my asphalt shingles were falling many years before they should. This conversation gave birth to my Roofing Ripoff book that you might want to read.
I decided I would never again trust the asphalt shingle industry. You get just one bite off the apple with me in most instances. I wasn’t about to take a chance on my next roof. I wanted a material that would last for 100 years, or more.
Metal and Plastic Alternatives
I had lots of options to consider after I had kicked asphalt shingles to the curb. I already knew that metal roofing was superb. There are many different styles. Interlocking metal shingles made from rust-proof aluminum caught my eye. A neighbor just down the street from me used them on his house and they look great.
Synthetic slate is what I decided to use. There are two USA manufacturers of this stunning material: DaVinci and Brava. The virgin vinyl used to make these shingles is thick. The colors and styles you can choose from will stun you. If you like the look of a shake roof, it’s available in this virgin-vinyl material.
I installed my 42 squares of DaVinci Roofscapes synthetic slate shingles myself. The synthetic slate installs just like regular asphalt shingles. In some ways, they’re easier to install than asphalt. You need to create a 3/8ths inch space between adjacent shingles. This spacing is required for expansion and contraction. It doesn’t need to be perfect. In fact, if the gap is a bit wider or a fraction less, it makes the roofing look more realistic.
Watch this video to see my completed roof.
Every person who has visited my house, including those making deliveries, says the same thing, “Holy cow, that’s a gorgeous slate roof.” I have an extra shingle next to my garage door I show them. Each person is stunned when they discover the roof is plastic.
My newsletter subscribers followed my re-roofing adventure years ago. Many have reached out to me asking how the roof has held up and how it looks with almost a decade of wear.
The roof looks as good as the day I installed it. In fact, it looks better in my opinion as the vinyl looks more like real dusty slate each day. The harsh ice and snow has done nothing to harm the roof.
I was a real estate broker in Ohio for 20-plus years before moving to New Hampshire. I know for a fact my synthetic slate roof will add tens of thousands of dollars of value to my house when I do sell. Re-roofing costs are in the stratosphere. The next owner of my house will never have to install a new roof.
The new owners will be shocked to discover I installed an ice and water barrier over the entire roof area before installing the synthetic slate. I know I’ll never have an ice dam leak or a leak from a wicked Nor’easter that blows several times a year.
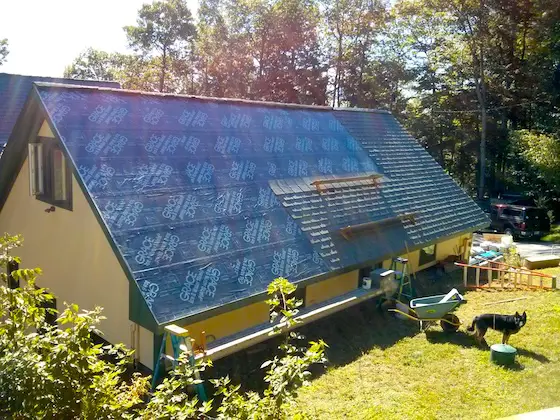
This is my garage roof. I installed Grace on the entire roof. Photo credit: Tim Carter Copyright 2024
Column 1579