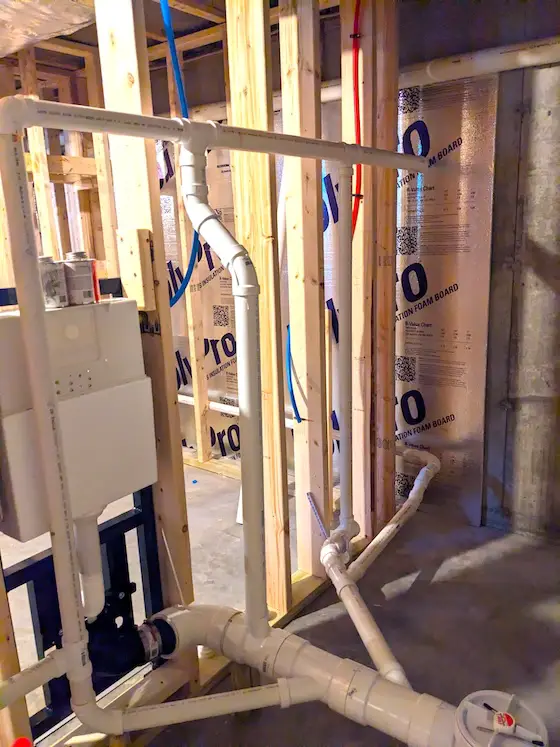
How to Add a Bathroom - You normally never see the pipes that carry wastewater away from a bathroom. This is a rare instance of a basement bathroom where the sewer line exits the house about 7 inches above the concrete floor. Copyright 2024 Tim Carter
How to Add a Bathroom
You may or may not know this, but I’ve been a master plumber for nearly four decades. I used to do all the plumbing in all the houses I built and in the remodeling jobs that had a plumbing component. I want to let you know if you’re thinking of adding a bathroom to your existing home that’s it’s not as hard as you might think.
Plumbing is Very Complex
Plumbing is indeed a three-dimensional puzzle. That’s one of the reasons I was intrigued by the challenges each job presented to me. I use my talents now to draw 3D riser diagrams for homeowners, architects, and business owners who need a permit. Plumbing departments all across the USA require riser diagrams. The diagram tells the plumbing department that you know the correct pipe sizes for all the drains and vents. The drawings also show how to connect all the pipes together.
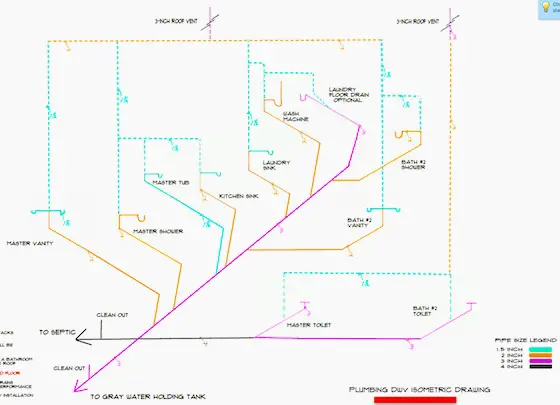
Here's a riser isometric drawing showing the separation of gray water from black water in a home. CLICK or TAP HERE to have me draw your riser diagram.
The raging inflation mixed with the high labor costs I’m seeing all across the USA have more and more homeowners like you attempting to install plumbing on your own. I may be one of the few plumbers that applaud this. While you need to have a good grasp of the plumbing code, it’s possible you can successfully install the drains and vent pipes for a typical bathroom. It may seem daunting, but allow me to pull the curtain back so you can see just how easy it might be.
While I no longer do plumbing for customers, my kids tug on me to put my skills to work on a regular basis. I’m in the midst of helping my son finish off his basement. We were able to include a full bathroom that will add lots of value to his home. Bathrooms are prized by most people looking for homes. You can verify this talking with a top-producing real estate agent in your city or town.
Pipe Sizes Matter
Here’s what you need to know about adding a bathroom in your home. First, a single 3-inch-diameter pipe is required. This pipe will connect to the toilet and the wastewater from a shower, tub, and one or more vanities will connect to this pipe as well.
In fact, the plumbing code allows up to two toilets to be connected to one 3-inch pipe that eventually connects to the larger 4-inch building drain in a crawlspace or under a basement slab.
Showers require a 2-inch drain pipe. Bathtubs and vanities are allowed to drain into a 1.5-inch pipe. That said, I prefer to install a 2-inch pipe for tubs. It’s so much easier to send a drain-cleaning snake down a 2-inch pipe rather a smaller 1.5-inch pipe.
Use Wyes not Tees
It’s important to realize that when you connect drain pipes that you use a wye fitting. A wye fitting looks much like the letter Y. In many ways it resembles how streams connect to larger rivers. You’ll typically see a stream enter a larger river at a 45-degree angle. This is how the blood vessels in your body work too. This angle forces the water downstream in the piping system.
Sanitary Tees Create Waterfalls
You can use fittings called sanitary tees for plumbing fixtures. Think of a sanitary tee the way you’d think of a waterfall out in nature. A river is flowing horizontally and all of a sudden the water goes over the edge to fall vertically.
The vanity in your new bathroom will undoubtedly use a sanitary tee. You can sometimes find them under a tub or shower too. Toilets can employ a sanitary tee as well so long as you have enough room to make one work. They work well where the vertical stack (waterfall) is within 3 feet of the toilet.
Venting Confuses Most Homeowners
If you decide to tackle a bathroom project yourself, I think you need to focus your attention on the vent pipes for all the fixtures. Vent pipes are a mystery to most homeowners. Each fixture requires a vent pipe.
The purpose of the vent pipe is to supply atmospheric air back into the system once wastewater is sent down the pipes. Think about your plumbing pipes before you flush a toilet. The pipes are just filled with air before you use the toilet. When you flush the toilet, you inject lots of water into the 3-inch pipe. This water pushes the air in front of it as the water makes its way to the sewer or septic tank. The air must be replaced and the vent pipes do this with ease if you size them correctly.
Not only do the vent pipes need to be sized correctly, but they also need to be in specific locations with respect to the location of the actual plumbing fixtures. This is all covered in the plumbing code but you may find it mind-numbing to read about them. I created a How to Vent Plumbing video for you. It’s on my www.AsktheBuilder.com website. I feel it does a splendid job of showing you all of this vent magic.
I want you to consider doing your own plumbing. It’s very fulfilling and there is a multitude of great information you can draw upon out on the Internet. You can also get on the phone with me if you feel you want a concierge plumber by your side!
CLICK HERE to have me CALL YOU ON THE PHONE or do a VIDEO CALL.
Column 1570