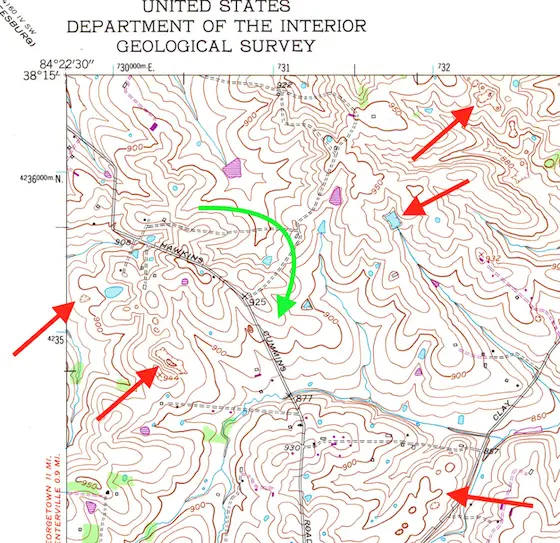
This topographic map should get your attention. The red arrows point to sinkholes that can cause serious structural damage to the average home. Copyright 2024 Tim Carter
Avoid Geologic Hazards When Building or Buying Land
You probably don’t give much thought to the ground under or around your home. What follows are a few true stories that may change your perspective. If you’re in the market to purchase land to build your dream home or are looking to move to purchase an existing home, what I’m about to share could prevent financial ruin. My college degree is in geology and the knowledge I attained allows me to look at building lots through a different lens than you might use.
Less than a week ago a woman hired me to do a one-hour video call. She recently purchased raw land in the heart of the Bluegrass region of Kentucky just east of Lexington. I happen to know this part of Kentucky is one of the top places in the USA for Karst topography. This translates to sinkholes that can cause serious structural damage to homes.
Before the call, I asked for the address. I wanted to locate her land on a US Geological Survey topographic map. You can get high-resolution PDF copies of these for free online for any land in the USA. Sure enough within a half-mile radius of her land there were no less than ten sinkholes. You can clearly see these on a topographic map as circles or ovals that have small lines pointing to the center of the circle or oval.
Does this mean her new home will sink into the ground? Not necessarily. That said, it might be a good idea to chat up the local building inspector or folks at the Kentucky Geological Society. I’d also inspect the land to see if there was evidence that a sinkhole had been filled in to disguise it.
Building on Buried Trees
Topographic maps can shed light on many things. My friend Ed purchased a lot in a new subdivision in Cincinnati, Ohio about twenty years ago. The developer had to do lots of cut and fill. Ed’s lot was land that was fill dirt. The dishonest excavator dumped dirt on fallen trees to bury them. Within a year after Ed’s house was built, it started to crack in half. The basement floor looked like a dough bubble on a pizza. The entire foundation was dropping but the floor was not falling at the same rate. Ed now knows to never again build on fill.
Flash Flood in Amberley Village, Ohio
About thirty years ago neighbors of mine were almost killed in a flash flood. They purchased a home in a nice subdivision nestled on rolling land. Their home was right on top of an old dry creek. Under their driveway was a hidden 5-foot-diameter storm sewer that was installed when the farmland was converted to residential property. My neighbors had no idea this pipe was in the ground.
One day a huge storm caused storm water to completely fill the pipe and then run across the land to a depth of 8 feet in my friend’s driveway. It completely flooded their basement in a matter of minutes. Had they studied a topographic map before buying this home, they could have seen from the contour lines how much land above them collected water and then funneled it to their lot.
New Madrid Earthquake 1811-12
Active geologic faults can be found all over the western USA. The center of the USA is not immune from tremendous earthquakes. In 1811-12 the New Madrid earthquake caused massive damage where western Tennessee touches southeast Missouri and northeast Arkansas. If you live near here or intend to build there, talk to your insurance agent about an earthquake rider on your homeowner’s policy.
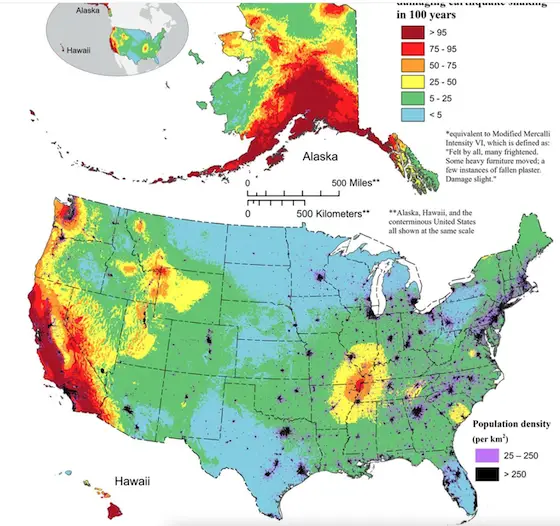
This is the 2024 US Geological Survey earthquake hazard map. CLICK it for a bigger version and more information. You can see the risk of huge earthquakes is high in the western Tennessee area. Public Domain Usage - Created with US taxpayer $$$
Landslide Causes a Propane Explosion
Landslides can also cause nightmares and death. Just three years ago two friends of mine died when a propane explosion destroyed their home. CLICK HERE to read one story about the tragic event.
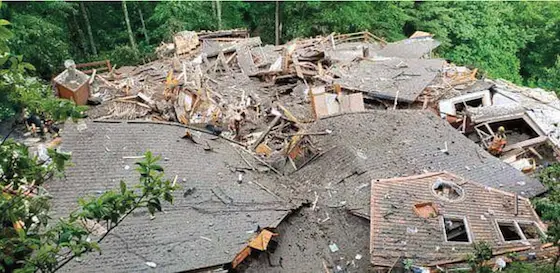
A propane explosion leveled this home in less than five seconds killing Jim and Audrey Landford. They were friends of mine. Copyright Boone NC Police Department Fair Use Doctrine Public Property
Heavy rain caused a landslide that dislodged their propane tank resulting in a gas leak in their home. This was preventable to a large degree but the average person would never think about the relationship of a propane tank to a hillside.
Cincinnati Landslides
Humble Cincinnati, Ohio is the epicenter of some of the highest landslide damage in the USA. The media darling for landslides is California where each winter we seem to see houses falling into the ocean during fierce winter storms. But in Cincinnati, the bedrock geology is such that thousands of homes are built on unstable clay soil that can be found on the hillsides all around the Tristate region. Watch this documentary film about Cincinnati Landslides.
Dry Land - No Water
How disappointed would you be if you purchased raw land only to discover there’s no water? Yes, this happened to friends of mine in Washington state. They had to stop drilling after boing a hole 700 feet. This might have been avoided had they talked to well drillers before buying the land. The drillers might have told them land to avoid and the places where water is discovered at a shallow depth.
You may place your trust in government officials in situations like this. That would be a grievous error on your part. There are neighborhoods in many cities in the USA that get flooded in periods of heavy rain. These old creek beds should have never been allowed to be developed by not-so-wise government officials.
You can make the best decision when buying land by hiring a professional geotechnical engineer or a professional geologist. These folks can look at raw or developed land and produce a report indicating any potential issues that could affect your major investment. I wish you the best of luck!
Column 1543